Li-ion cell testing and selection
Li-ion cells are the foundation of any ebike battery pack. They come in various shapes, sizes, capacities, voltages, and discharge rates. The battery chosen for your ebike battery is determined by your specific requirements and preferences, such as power output, energy density, cycle life, safety, and cost.
There are several types of li-ion cells currently on the market, but the most common ones used in ebikes are cylindrical cells 18650 and 21700, usually with NMC or NCA chemistry. This is because these batteries offer the highest energy density.
Some factors we consider when testing and selecting li-ion cells are:
- Capacity/energy: The amount of charge a cell can store and deliver at a given voltage. It is expressed in amp-hours (Ah) or watt-hours (Wh). The higher the energy, the longer the ebike’s range.
- Discharge rate: The rate at which a cell can deliver current at a given voltage. This is measured in amps (A) or C-rate (the ratio of current to capacity). The higher the discharge rate, the faster the acceleration, plus high discharge rates allow for better hill climbing (assuming the motor is powerful enough).
- Energy density: The amount of energy a cell can store per unit volume or mass. It’s measured in watt-hours per litre (Wh/L) or watt-hours per kilogram (Wh/kg). The higher the energy density, the lighter and smaller the battery can be.
- Cycle life: The number of times a cell can be fully charged and discharged before its capacity drops below a specific threshold, usually 80% of its initial value. The higher the life cycle, the longer the lifespan of the battery.
- Safety: The ability of a cell to withstand trauma or damage without causing fire or explosion. Safety depends largely on chemistry and structure, along with the protection mechanisms incorporated into the cell. Some chemistries are stabler than others and some structures are more robust than others.
With so many factors to consider, an ebike battery manufacturer can’t simply rely on data from cell suppliers. Instead, they should test and validate performance independently for any given application. At EMBS, we have a complex cell testing program, carried out in both our in-house laboratory and in external labs and universities.
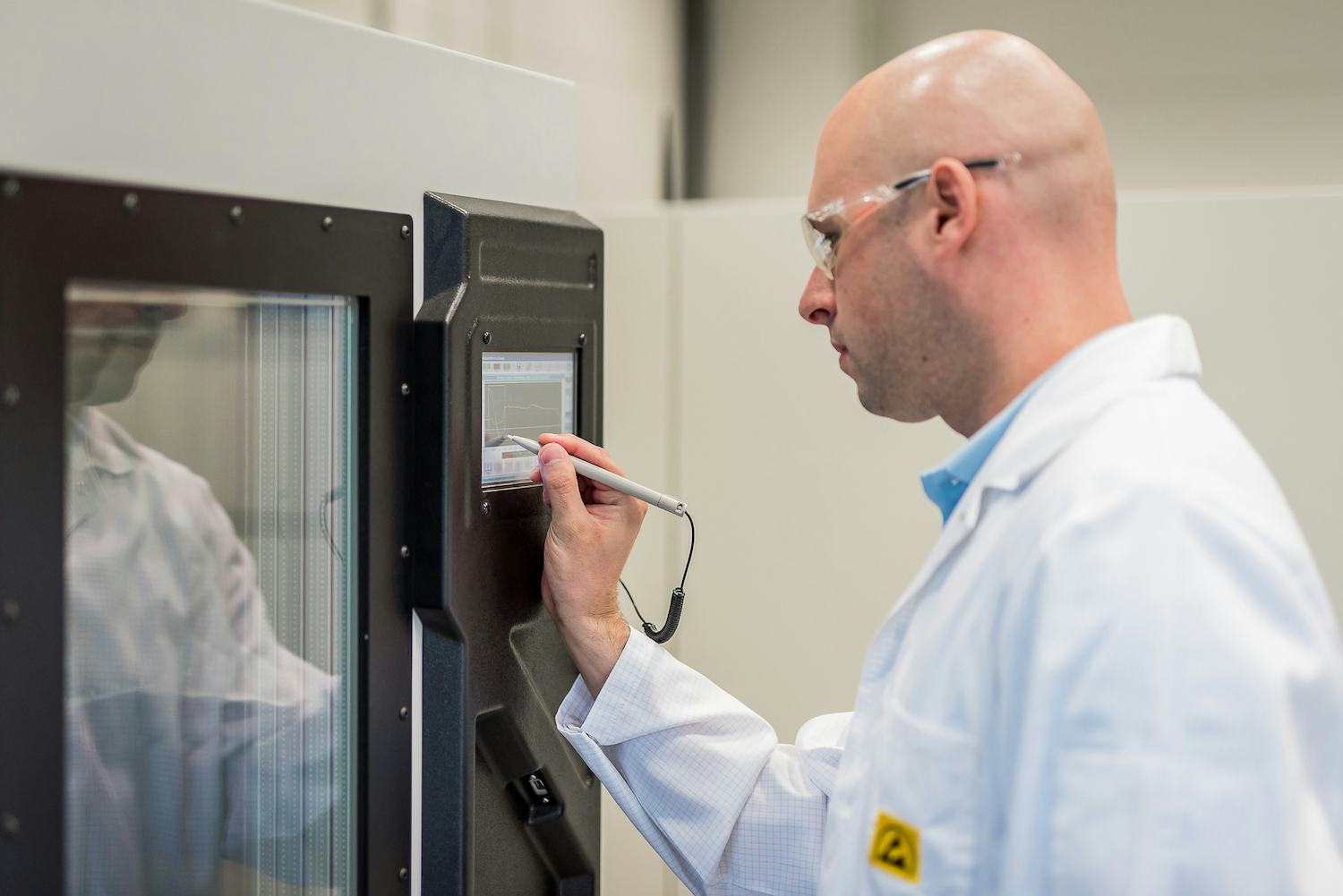
Custom made BMS and electronics
A battery management system (BMS) is a device that monitors and controls various aspects of an ebike battery pack, such as voltage, current, temperature, state of charge (SoC), state of health (SoH), and cell balancing.
A BMS can protect the battery from overcharging, overdischarging, overcurrent, overtemperature, and short circuits. It can also communicate with other devices on the ebike, such as the controller, display, or charger. It is vital to protect the BMS from damage and against moisture.
A custom-made BMS can have many advantages over a generic or off-the-shelf system, such as:
- It can be tailored to fit the specific cell type, configuration, and performance requirements.
- It can offer more features and functions, including data logging, diagnostics, and smart charging.
- It can be integrated with other electronics on an ebike, including sensors, switches, LEDs, and connectors.
- Any modifications requested by the customer can be carried out quickly by the battery manufacturer.
Designing and building a custom BMS requires complex knowledge and skills in electronic engineering, programming, and PCB design. Therefore, it’s vital to partner with a battery manufacturer experienced in this field.
Optimal mechanical design
The mechanical design of an ebike battery pack refers to the shape, size, structure, and arrangement of the cells and other components within a casing or enclosure. Mechanical design influences performance, safety, durability, and aesthetics of the battery. Some factors to consider when creating an optimal mechanical design include:
- Space: The amount of room on the ebike frame or rack for mounting a battery pack. This can limit the dimensions and configuration of the battery pack and might require sophisticated solutions, such as jak flexible printed boards.
- Weight: Using proper materials and an optimal shape can significantly reduce the weight of a battery, while still providing the required robustness.
- Protection: The battery pack must be well protected from external factors, such as impact, vibration, moisture, dust, and heat. This can be achieved using a sturdy and waterproof casing, as well as padding, cushioning, and shock-absorbing materials. Protection can be enhanced by adding fuses, SCP, or other safety devices to prevent overvoltage, overheating, and overcurrents.
- Cooling: The cooling of the battery pack from internal heat generation due to charging or discharging. Cooling can be achieved by using materials with high thermal conductivity, such as aluminium or copper, for the casing and connectors. Cooling can be further improved by adding heat sinks to dissipate heat from the pack or BMS.
- Serviceability: An optimal mechanical design should be achieved without extensive potting and filling materials or permanent glue, which would prevent battery servicing.
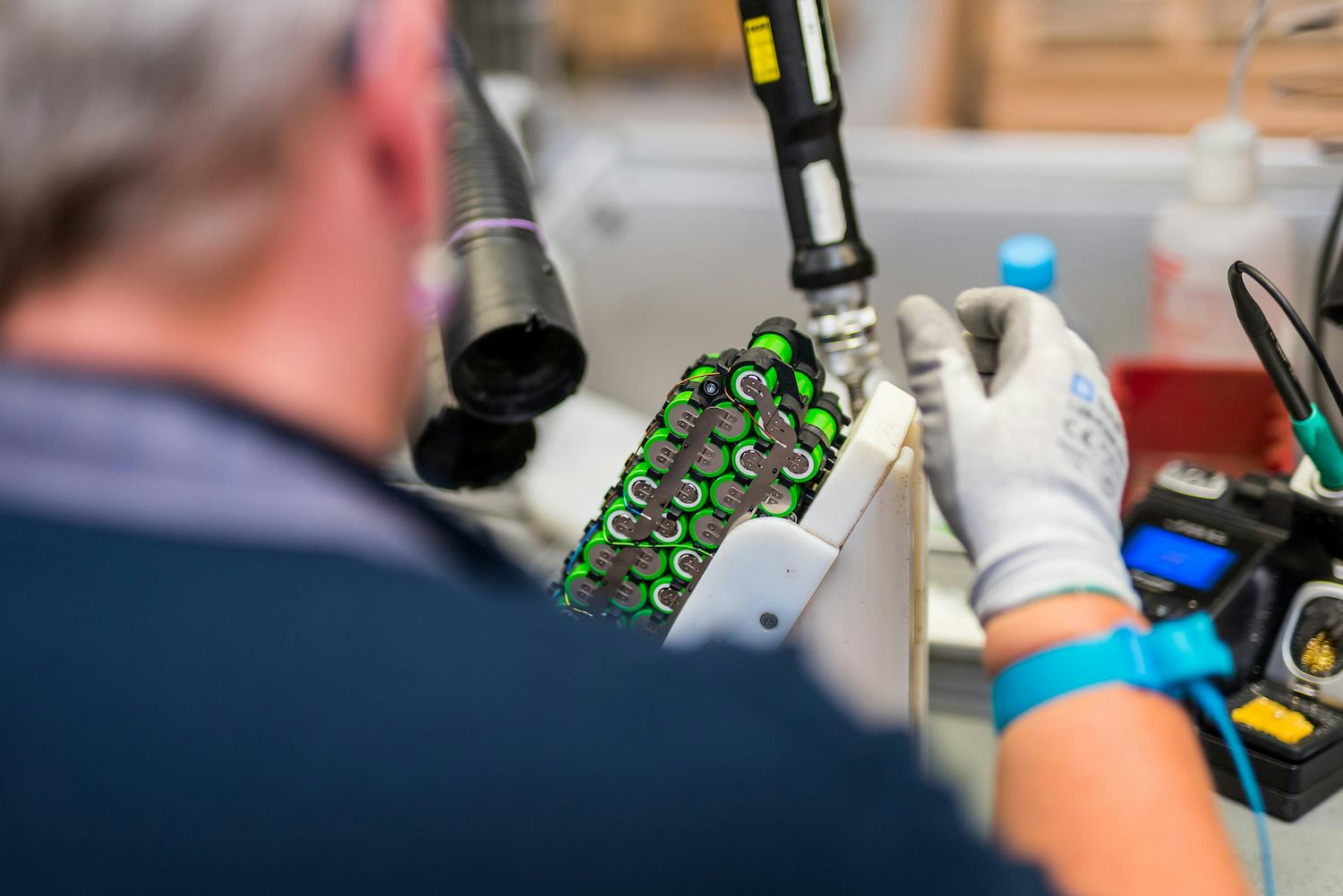
Proper procedures for mass production
Every battery design must be optimised for serial production, a factor that should be considered from the earliest phases of the project. Additionally, mass production of ebike batteries requires proper procedures to ensure high quality and consistency. Some vital procedures include:
- DFMEA/PFMEA: Required to ensure all predictable risks for design and process are addressed.
- Cell sorting: Should be sorted with accordance to production batches and be graded according to their voltage and internal resistance before assembling them into packs. This ensures cells with similar characteristics are grouped together, potentially improving balance, performance, and lifespan.
- Spot welding: Well selected welding parameters must be used to ensure strong and reliable electrical contact between cells and reduce resistance and heat generation. Low quality welds are prone to vibration and can significantly reduce the expected lifespan of a battery.
- Testing: It’s vital to test incoming components and each battery pack on an End of Line tester. This ensures that each pack meets its specifications and performance standards, and that defects and faults are detected.
Design validation process
Design validation is the process of verifying that an ebike battery design meets its intended purpose and requirements. It can be done via various tests and experiments on prototype models or samples of the battery pack under realistic conditions.
Experienced battery manufacturers create complex DVP&R (Design Validation Plan & Report) to be followed on each stage of product development. The results of tests are documented in appropriate reports.
Some aspects of the initial pre-validation can be completed during the early stage of design by performing thermal and mechanical simulations. This influences some of the design decisions, making sure the final product will pass validation and certification without issues or requirements to redesign. This contributes to fast project realisation.
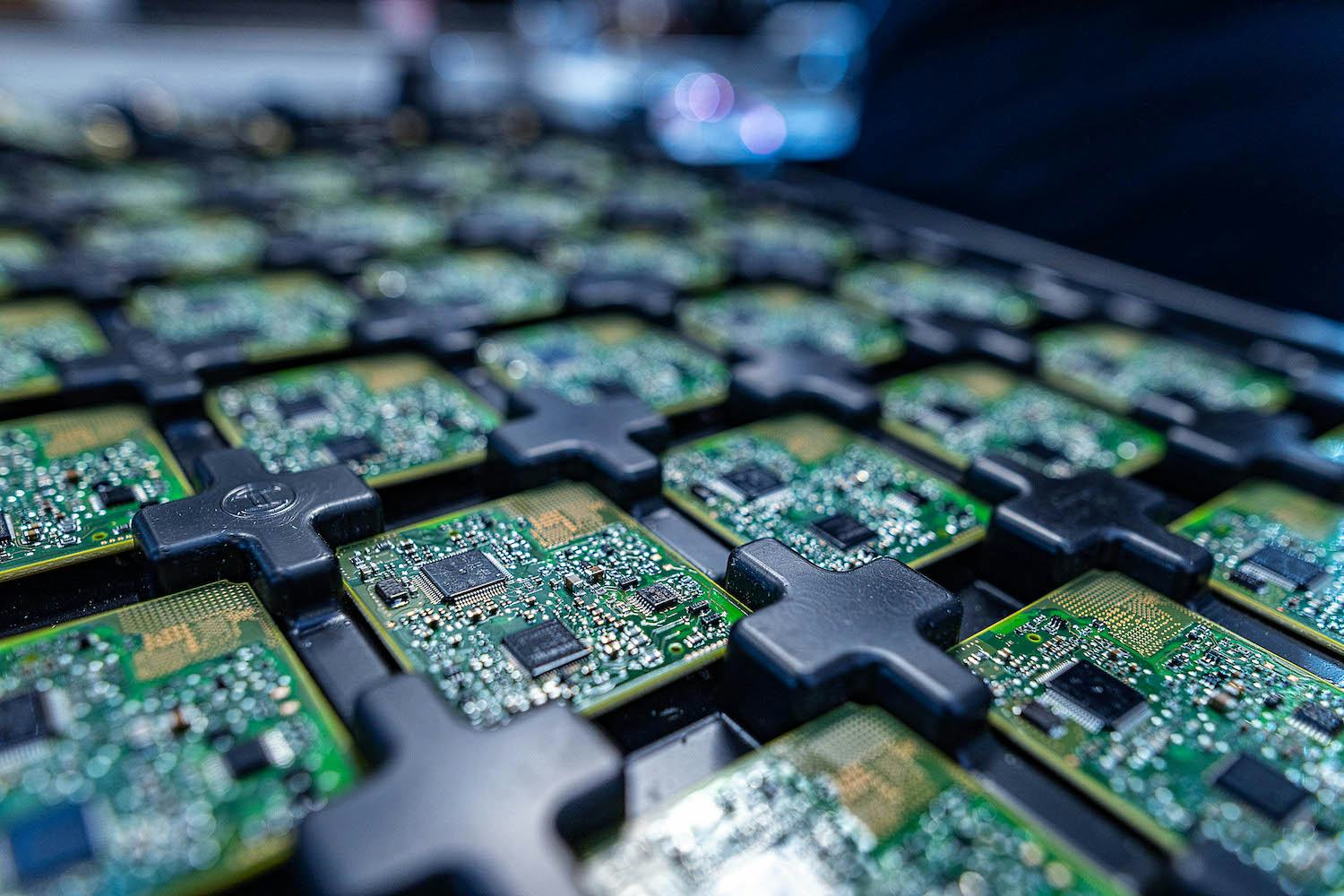
Product certification for target markets
Product certification is the process of obtaining approval or recognition from relevant authorities or organisations, which permits the ebike battery to be sold or used in a specific market or region. Gaining product certification involves complying with certain standards, regulations, laws, or guidelines that govern the quality, safety, performance, or environmental impact of the battery.
Product certification can also involve the testing and inspecting of the product by accredited third-party laboratories or agencies to verify its compliance and quality.
The certification of ebike batteries is an important and necessary step, and it’s vital that a battery manufacturer has the facilities in place to conduct tests, like UN 38.3, internally, and that they’ve established partnerships with external certification bodies to ensure a smooth certification process for CE and/or UL marking. This will contribute towards the battery being brought to market without undue delays.
Conclusion
Ebike batteries are complex products that require careful design and production to ensure optimal performance, safety, and durability. By choosing a manufacturer that follows best practices, you can be assured that your ebike battery will meet your expectations and requirements, plus pass certification without issues. The whole process should be smooth and timely, and result in the delivery of the highest quality product.
About EMBS
EMBS is a world leader in the design and manufacture of li-ion batteries for e-bikes. From their base in Poland, they produce a variety of e-bike batteries, along with batteries for several other appliance types.
This article is sponsored by EMBS.