These upgrades, integrated into Ananda’s strict quality control protocols and certifications, are designed to speed up production at the Wuxi factory while enhancing quality assurance. This investment strengthens Ananda’s commitment to being a trusted partner, delivering high-performance, reliable e-drive systems.
Comprehensive quality control
The Wuxi factory, located two hours Northwest of Shanghai, is the company’s primary mass production site for hub and mid-drive motors, HMIs, sensors, and controllers. Every product undergoes both laboratory and field testing before entering the market. Comprehensive quality control protocols cover a wide range of tests, including low-temperature, ESD (electrostatic discharge), thermal, vibration, mechanical shock, humidity, torque, and salt spray testing. Final Quality Control (FQC) ensures that each finished product meets all required specifications through detailed visual inspections and functional testing.
Outgoing Quality Control (OQC) further verifies that all components are correctly assembled, accurately labeled, and properly packaged prior to shipment. Every product is equipped with a traceable barcode compatible with EPR (Extended Producer Responsibility) systems and is verified and tested in collaboration with TÜV to ensure impartial quality validation.
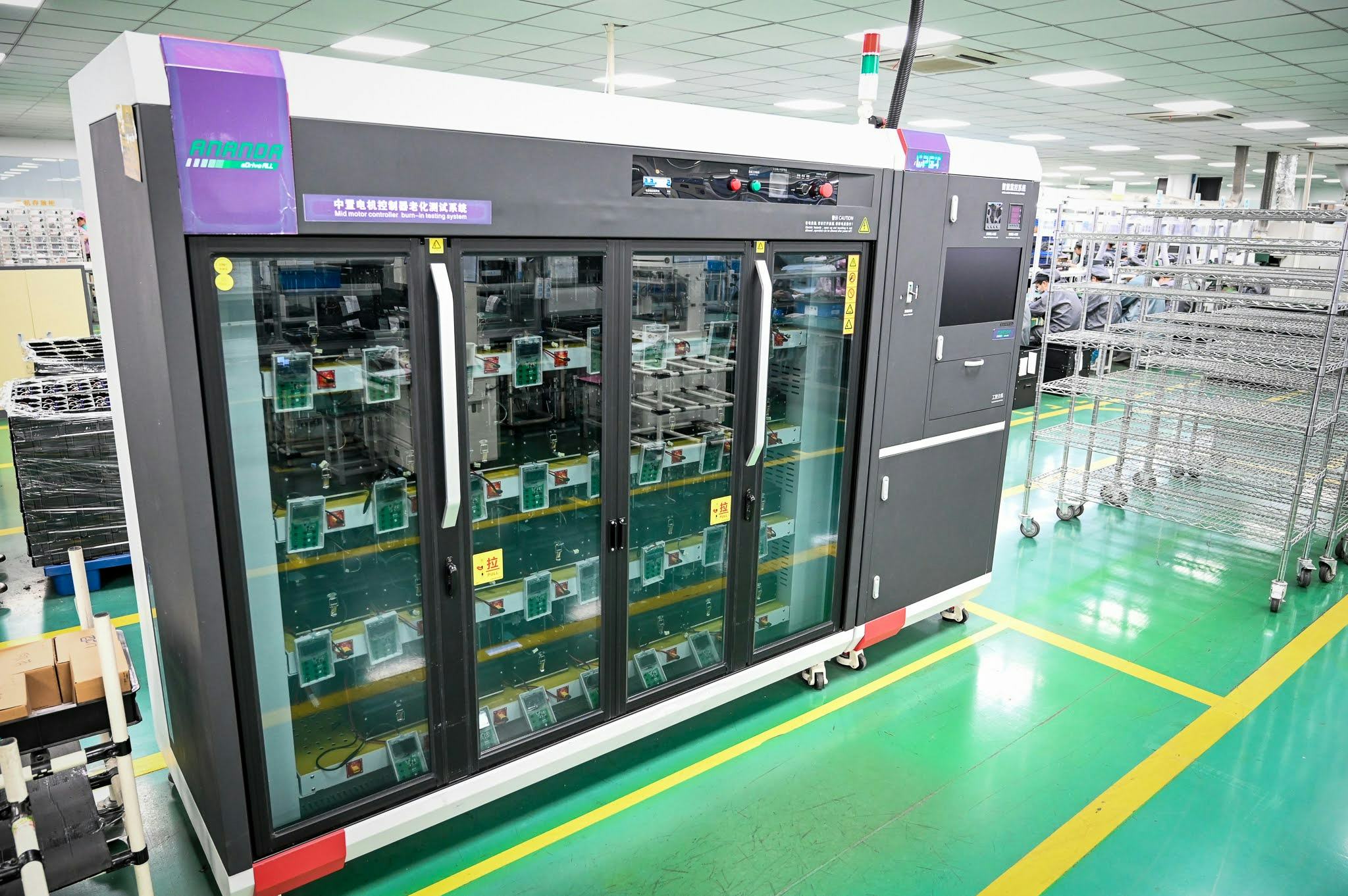
New testing tools
Over the past few years, Ananda has increasingly established itself as a reliable partner in e-drive systems, working with renowned bicycle brands across Europe. “But in a fast-moving industry, standing still is not an option,” says Chao Liu, oversales director at Ananda. “Committed to continuous improvement, we continue to enhance our quality assurance processes by integrating numerous advanced testing equipment and efficient machinery for e-bike motors and control systems.”
Among the newly introduced machines is the In-Circuit Tester (ICT), a high-precision automated test system integrated directly into the controller production line. This allows early detection of any potential PCB issues before firmware programming or final assembly takes place. Another key addition is the Controller Aging Test equipment, which simulates years of real-world usage in a short timeframe to ensure long-term performance and reliability. Other newly added equipment are a servo press, an NVH (Noise, Vibration & Harshness) testing system, a mid-drive motor tester, and an automatic PCB depanelizer.
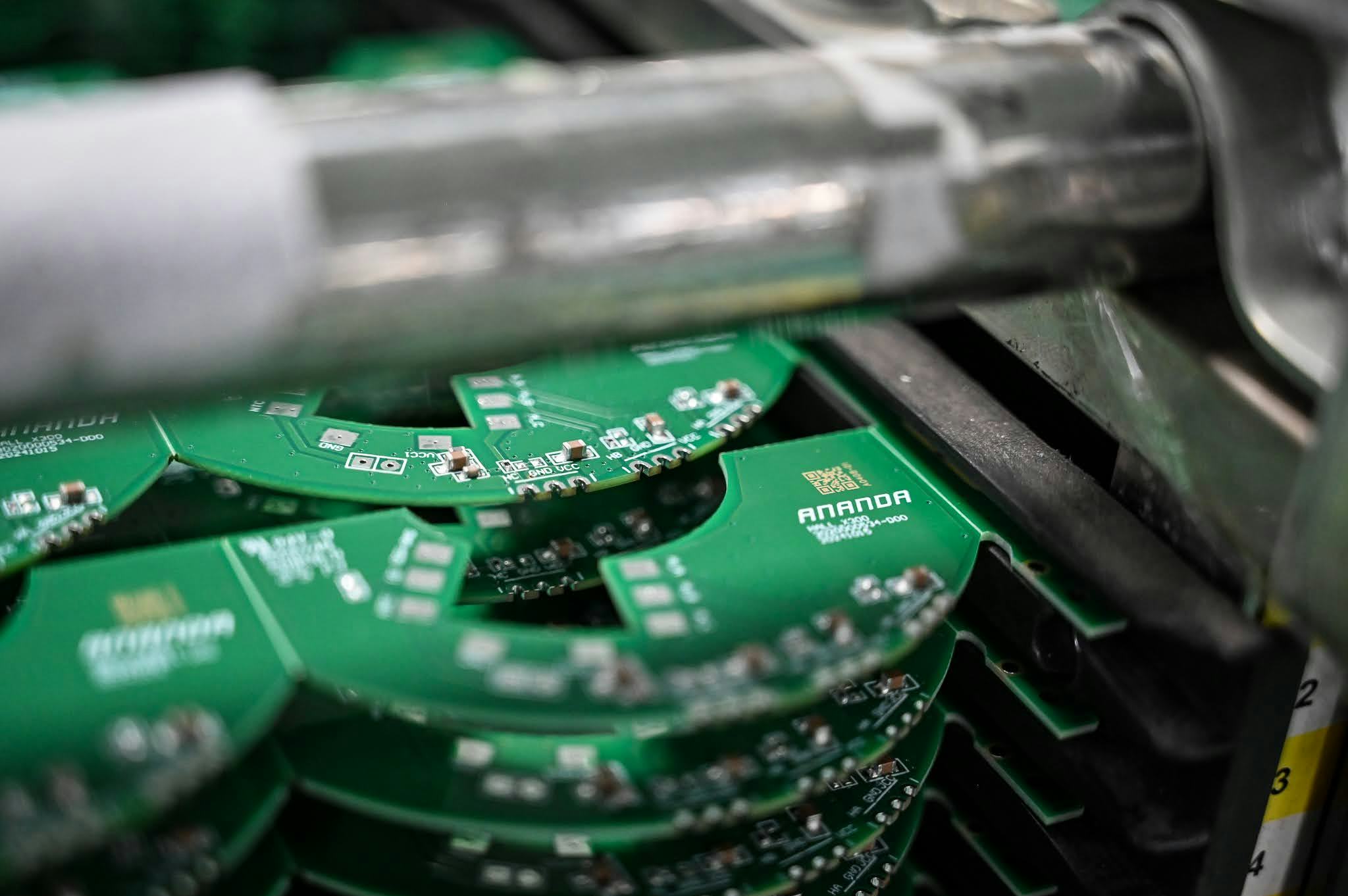
Smart processes for long-term reliability
By integrating these machines into the production process and increasing the use of iterative testing, Ananda gains even greater control over production quality. If a component or product does not meet the required specifications, it is sent back to the beginning of the production line for correction. “This ensures that new products developed by the R&D department, already extensively tested in the lab for waterproofing, noise levels, performance, torque, vibration, and more, also meet the strict reliability standards during full-scale mass production. These new investments reflect our commitment to building long-term confidence with our customers by delivering reliable, thoroughly tested systems, every time”, says Liu.
This article is sponsored by Ananda.