Ergonomics and Space Optimization
Leveraging over fifteen years of expertise in the bike assembly industry, Machontrol places a dual emphasis on performance and the vital elements of ergonomics and space optimization in the assembly environment. Engineered with ergonomic principles, their machines deliver a comfortable and efficient working experience for operators.
The user-friendly interface and intuitive controls not only minimize operator fatigue, but also maximize productivity. Furthermore, the compact design enhances floor space utilization, enabling manufacturers to fully optimize their assembly areas. Additionally, the mobility of these machines provides flexibility in adapting to various production setups, reinforcing their role as dynamic solutions in the evolving landscape of bicycle manufacturing.
Energy Efficiency and Data-Driven Operations
We all understand the importance of energy efficiency in today's environmentally conscious world. Our machines are designed to minimize energy consumption without compromising performance. Smart technology and advanced algorithms optimize power usage, ensuring energetically efficient operation throughout the assembly process. Moreover, the machine's integrated data collection capabilities enable manufacturers to gather valuable insights, allowing them to analyze and optimize their production workflows based on real-time data.
Effective communication is paramount in any assembly process. These machines boast integrated advanced communication features that foster seamless collaboration among management, operators, and machines. The user-friendly interface and intuitive controls facilitate effortless programming and monitoring of parameters. This streamlined communication not only diminishes the risk of errors, but also elevates overall efficiency. Additionally, the capability to transmit data to the machine signifies a proactive approach to minimizing mistakes and continuously refining the production process
Fork Cutting Machine: Cutting Edge Efficiency
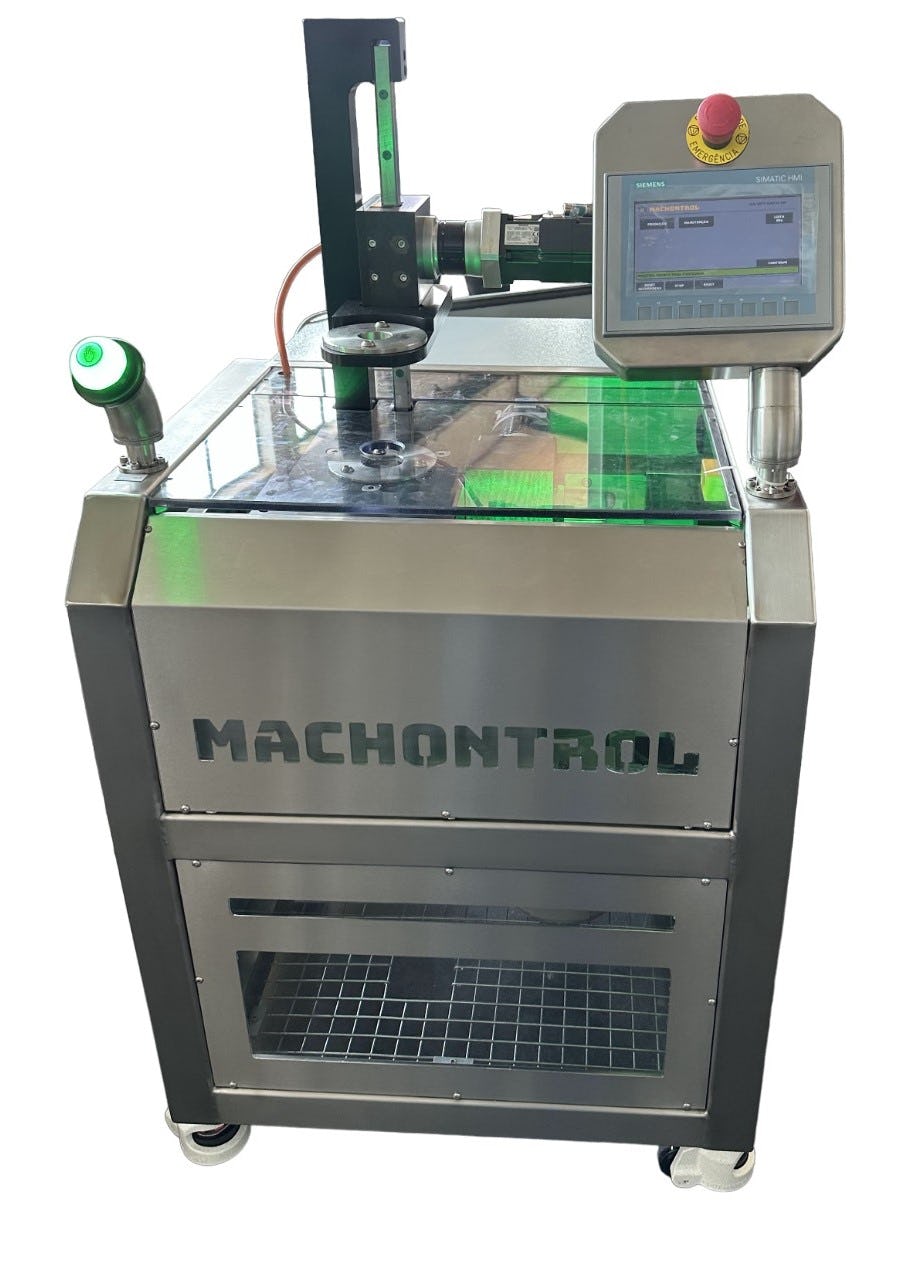
The Fork Cutting Machine ensures accurate, silent, and consistent cuts, resulting in a smooth and polished finish. This powerful machine features state-of-the-art technology, providing a robust cutting and measuring mechanism, cutting through different fork materials with ease and precision. The holding fixture ensures stability, accommodating diverse fork sizes without requiring tooling changes.
Bid farewell to imprecise cuts and uneven edges. This machine guarantees exact and uniform cuts, contributing to a flawless assembly process. It also features a chamfering process that removes rough edges and burrs from the cut surface of the fork. The servomotors provide unparalleled control, ensuring precise positioning and consistent cuts, minimizing errors, and eliminating the need for rework, ultimately saving valuable time and resources.
Fork Head Cup and Star Nut Press: Cutting Edge Precision
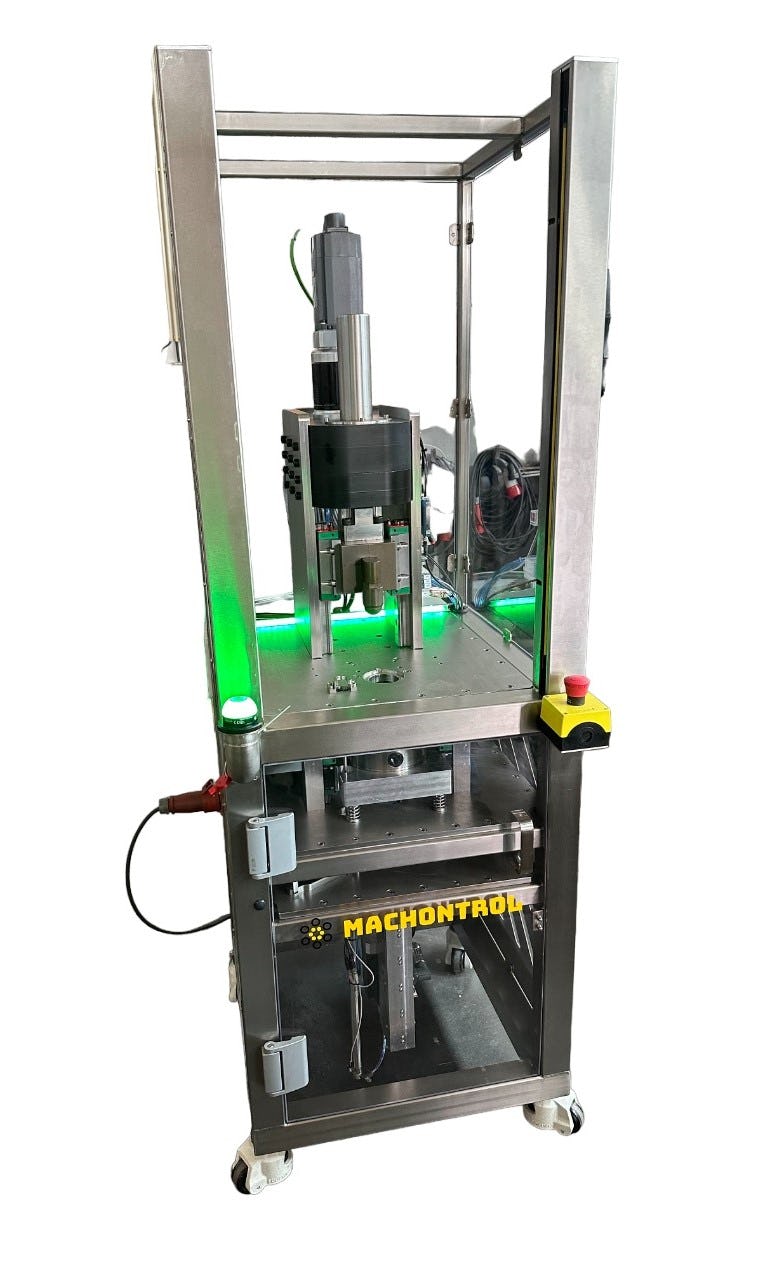
A revolutionary solution ensuring the secure and precise installation of head cups and star nuts on forks. This high-performance machine delivers consistent pressing power through servomotors, offering unmatched control for accurate component positioning.
For the longevity and safety of assembled bikes, precise installation of head cups and star nuts is paramount. The Fork Head Cup and Star Nut Press excels in delivering secure and accurate installations with its steadfast holding fixture, eliminating risks of misalignment or improper seating. Manufacturers can rely on this machine for meticulous and durable bike assembly.
Automatic Star Nut Feeder for Efficiency
In pursuit of efficiency, the Fork Head Cup and Star Nut Press features an automatic star nut feeder, eliminating manual handling and reducing the chance of errors. This innovation ensures the correct installation depth and orientation of the star nut, providing manufacturers with consistent and reliable results. Streamlining production processes become a confident endeavor with the precision and efficiency of this installation process.
The transformation of bike machinery has profoundly reshaped the bicycle manufacturing landscape. These cutting-edge technologies provide precision, secure installation, energy efficiency, data-driven optimization, enhanced communication, error reduction, space optimization, and improved mobility. By integrating these innovative machines, bicycle manufacturers can elevate efficiency and quality, and meet escalating market demands. As the industry progresses, the incorporation of advanced bike machinery will be pivotal in defining the future of bicycle assembly.
This article is sponsored by Machontrol.