But where does innovation come from in turbulent times and how can new methodologies and technologies influence bicycle design in the future? Often the big brands themselves seek assistance from experts outside their field in order to stimulate innovation and new ideas.
Modern technologies and engineering methodologies
Service providers such as Radiate Engineering & Design roll up their sleeves and lend a hand to bicycle brands when it comes to product development. What makes them special is the application of modern technologies and engineering methodologies derived from their experience in sectors like aerospace or Formula 1. How does that work? Let’s take a look and find out!
Holistic Bicycle Development influenced by aerospace and Formula 1
“The application of knowledge from different fields such as the aerospace industry and Formula 1 has yielded impressive results in the development of cycling products,” explains Jonas Schmid, Head of Bicycle Engineering at Radiate Engineering & Design. “We have learned a lot from developing lightweight structures for drones or optimising the fluid flow for a twintip foil board”, adds Timothy Habermacher, CEO of the company. "These experiences, in combination with our dedication to simulation technology, set us apart from others," he concludes.
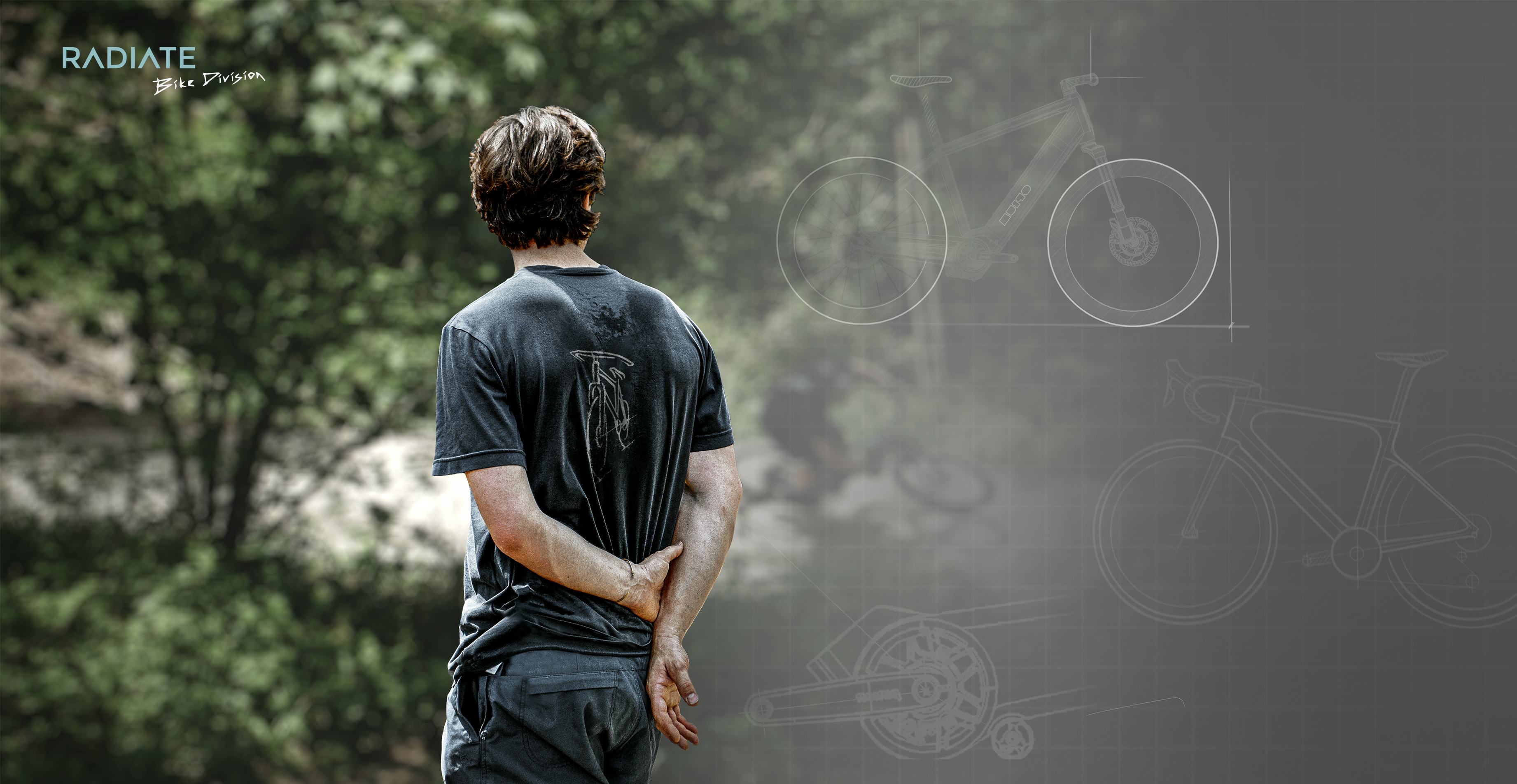
Whether it comes down developing a complete bicycle from scratch or just optimising the structure of a single frame or component – the engineers and designers from Radiate offer the whole range of services.
Bike Division
The expert team is set up in a special unit called “Bike Division” and consists of experienced specialists with a background from various disciplines such as Composite lightweight experts from aviation, fluid dynamic engineers with a background in F1 racing, and renowned industrial designers for two-wheeled and modern mobility design. The interdisciplinary team makes it possible to manage projects of a wide spectrum: from aerodynamic wheelsets to complex speed pedelecs to highly optimised lightweight composite handlebars.
“Functionality, design, materials, manufacturing processes as well as costs can not be viewed separately but need to be addressed holistically,” says Timothy Habermacher, CEO of Radiate Engineering & Design.
The importance of Industrial Design and parametric CAD / CAE Construction
When it comes to industrial design, the emergence and acceptance of new materials and technologies has shifted away from the old ‘form follows function’ principle. Modern production methods as well as the intensive use of fiber reinforced composites give the bicycle industry nowadays the opportunity to push new forms, patterns, shapes as well as functionalities. The correct use of these new designing possibilities is a refined play in knowing what to add and what to leave out. At this point, the benefits of a stringently structured parametric CAD comes into play. It allows early checks of feasibility and manufacturability, ensures the integration of mechatronics and components and allows automatic updates to the model if changes are made to the design – and this all along the product development cycle.

“Ultimately, a parametric CAD provides for a better quality product, which functions well and meets all performance requirements. Moreover, it makes the development process more robust, reliable, and cost-effective. That’s why we invest heavily in the best CAD possible, using state-of-the-art tools such as Siemens NX,” explains Jonas Schmid.
Digital twins and the power of simulation technology
Up to this point, the development of a bicycle component sounds very familiar: ideation, industrial design, some sketches and drawings which are later translated into a CAD that serves for the industrialisation. End of story? Far from it!
In the past, bicycle parts, such as a frame, have been developed according to this methodology: a brand will design the frame, pass it to a third-party manufacturer, who will develop the layup, a mold (or use an open mold) and produce a set of prototypes that hopefully meet the requirements and specifications. If not, time and cost-intensive rework and iterations have to be done. The benefits of modern simulation technology have fundamentally changed that.
Data-driven knowledge
Nowadays, it’s possible to incorporate data-driven knowledge early on in the product development process. A good example is the use of digital twins: “For useful structural optimisation, useful boundary conditions need to be defined. In order to optimise a bicycle or a component, we test and validate every design with digital twins against real-world load-cases and ISO norms. We also incorporate novel methods such as Machine Learning algorithms in order to iterate faster and reduce the amount of physical prototypes to the bare minimum. That way, a cost efficient optimisation is ensured, with no surprises after releasing the design for manufacturing,” says Timothy Habermacher.

Suitable for every product development process
Now you might think this method is only meaningful and profitable for high-end bikes and highly optimised structures for professionals and racing. But its absolutely the opposite. Radiate’s simulation-driven approach makes sense for every product development process. It doesn't matter whether it's a modern speed pedelec, normal gravel bike or simple commuter. Like this Radiate is pushing innovation, making products more robust and safer and at the same time shorten development cycles and failure rates.
"This isn't a fairy tale, but modern engineering, which unfortunately isn't given the attention it deserves by most bike brands. The majority still depend on knowledge from the Far East and waste a lot of innovative power, as well as valuable time to market," says Habermacher.
Prototyping, testing and validation under real-world conditions
Only after a bicycle or component performs digitally, the parts are released for validation. Based on the acquired knowledge through digital prototyping (made possible by structural simulations), Radiate undertakes a final validation test of sub systems or components under real-world conditions. With unique methods such as on-bike Data Acquisition, the experts of the “Bike Division” are able to record load spectra which are analysed, evaluated and eventually converted into input variables for further iterations and optimisation – digital and physical go hand in hand.
As Jonas Schmid puts it: “This is an integral part of our Simulation-Driven Engineering and Design approach and cuts down cost and time tremendously. No tedious loops with Asia, no communication barriers and the insights are much closer to the customer.”
Knowledge management leads to successful industrialisation
After the dust has settled on the development process, the final steps for a successful industrialisation have to be completed. Radiate helps its clients setting up a ramp-up strategy, facilitating decisions that lead to the best possible usage of time, financial means and resources. In order to achieve production targets, the bicycle experts accompany the sourcing and supply process as well as lead existing manufacturers with production and QC instructions.
“We have often experienced that production processes have to be rethought from the ground up, especially with regard to innovative new developments,” says Jonas Schmid. “That’s why transferring knowledge is an essential component in our projects. We provide our clients with an effective knowledge transfer process, making sure that a project or product is handed over correctly. For us, that’s the definition of a partnership on eye level,” adds Schmid.
“We share the passion for bicyles with our clients and look forward to continue to rethink how bicycles and bicycle parts are developed, applying modern technologies consequently in order to make innovation possible,” concludes Timothy Habermacher.
This article is sponsored by RADIATE