The high-end rim drilling station is capable of drilling the spoke holes into the rim from both the inside and outside and can even drill the valve holes from the outside.
What makes the machine special is its ability of drilling at any angle, the outer holes can be drilled in an Axial offset and the inner holes can be drilled both Axial and Radial with offset. This gives a lot of flexibility to drill the holes in any position, which in turn means that the spokes can be drilled perpendicular to the spoke angle. This has a positive effect on the nipple seating and screwdriver engagement. The spokes or nipples won’t bend this way, meaning that the spokes will have increased longevity and the wheel will be put under less pressure, thus increasing the final wheel quality. Not to mention perpendicular spokes will be much easier to lace for both man and machine.
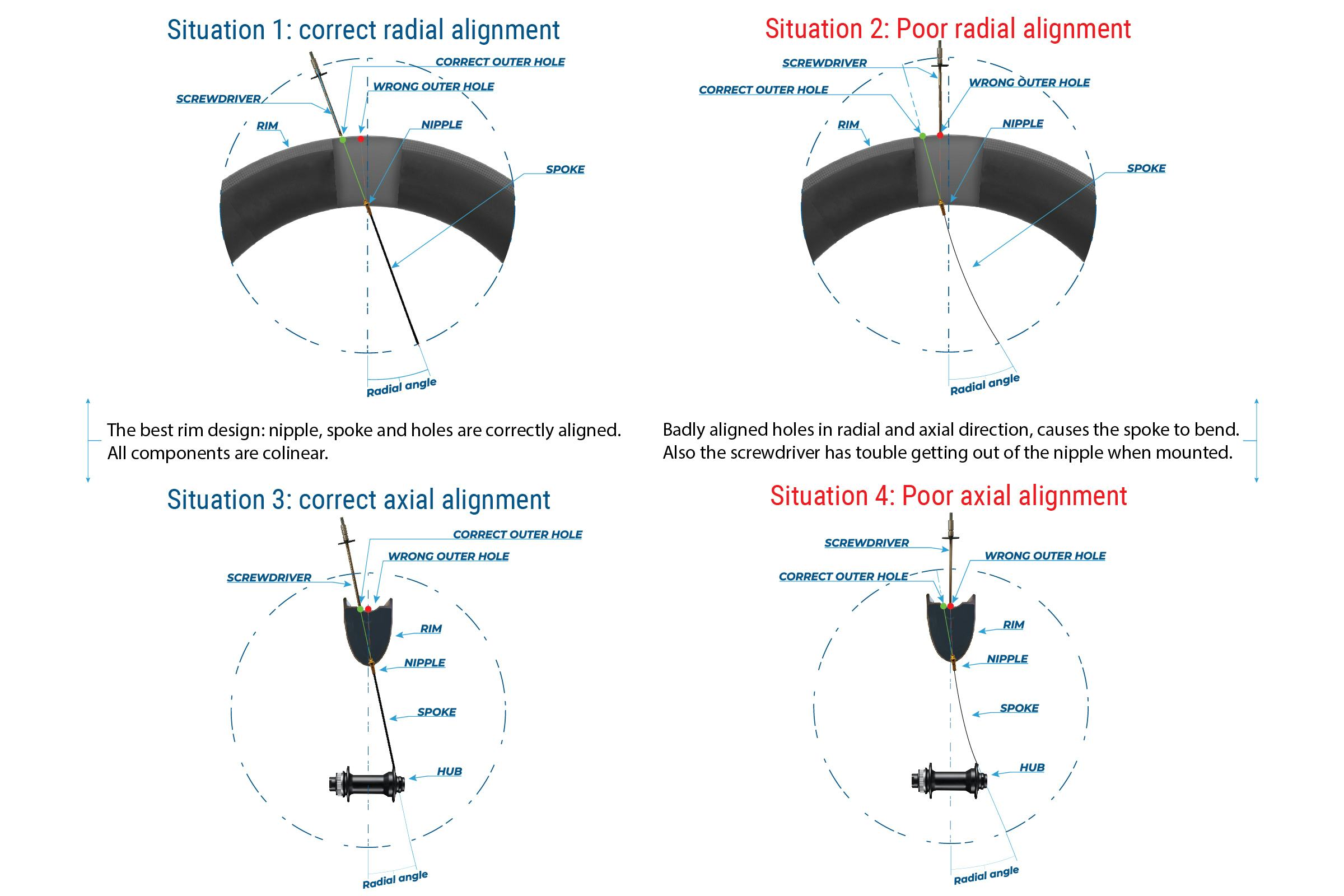
In-built vacuum cleaner
Drilling stations produce a lot of waste which can hinder the drilling process or influence the quality of the rim and even can be dangerous, if too much waste is present. Not to mention it takes a lot of effort and time to keep the machine and the surroundings clean. So, to make the machine as safe and user friendly as possible, the drilling process of the high-end rim drilling machine takes place in a closed compartment. In this closed compartment there is an in-built vacuum cleaner positioned at the drilling process to vacuum all, to even the smallest carbon dust/fibers particles. In case any waste is still found in the compartment, the in-built vacuum cleaner can be detached to clean this manually. The high-end rim drilling station ensures of a clean and high-quality product without a lot of maintenance.

Flexible setup
The high-end rim drilling station is not only capable of outputting high quality rims but is also very easy to use and has different configurations. The machine comes equipped with a pin to set the size of the wheels and a control panel to adjust additional processes, such as angle and drill speed.
The machine can handle standard drilling 26 inch (571 mm), 28 inch (633, 634, 635, 636, 637 mm) and 650 (595 mm). Minimum inner diameter 433 mm. Maximum outer diameter 637 mm. Minimum rim width 19 mm, maximum rim width 45 mm. For other sizes contact with the manufacturer is required.

The machine is also capable of handling abrasive environments as the machine comes equipped with heavy duty Kress milling motors. This in combination with the technology makes it possible to optimise for automatic wheel building. If you don’t have carbon wheels, the machine is available as high-speed rim drilling machines for aluminium rims.
When can you order the high-end rim drilling machine
If you are interested in the high-end rim drilling station and the features, the expected release date of the machine is mid-2023. You can however pre-order the machine at the manufacturer.
This article is sponsored by Holland Mechanics.